Auto light moulds generally use PC or ABS, which has good permeability, relatively high surface requirements, and the appearance can meet the requirements of highlights without other treatments. So how to make auto light mould?
Auto light moulds generally have the following characteristics:
-
1. Moulding temperature is high, generally around 80-90 degrees. Keeping pressure at a higher mould temperature is conducive to eliminating defects such as weld marks, flow marks, and product internal stress. Therefore, the mould needs to be heated when it is working. To prevent heat loss, a resin heat insulation board is usually added on the fixed mould side.
-
2. The surface of the mould cavity is extremely bright. The product produced by the auto light mould can be used directly for installation without any surface treatment. Therefore, it has high requirements for mould steel and plastic materials.
Main points of Auto light mould design
-
1. The light mould has strict requirements on the product structure. As we all know, the brighter the product is, the more sensitive it is to the refraction effect of light, and slight defects on the surface will be found soon. Therefore, how to solve the shrinkage problem is the primary problem of auto light products. According to empirical statistics, the thickness of the general product ribs does not exceed 0.6 times the thickness of the main glue position, and it will not shrink, or the shrinkage is small and it is difficult to be found and can be ignored. However, for auto light products, such requirements are far from enough, and the thickness of the product ribs needs to be reduced to no more than 0.4 times the thickness of the main glue position, and special treatment must be done for the screw posts.
-
2. The hot runner system is very important to the light mould. Whether a product with no weld lines can be injected, the quality of the hot runner and the adjustment of the machine are decisive factors. The characteristics of the hot runner system of the auto light mould: the hot nozzle of the auto light mould must have a sealing needle, and each hot nozzle must have an independent air channel it is not allowed to connect multiple air channels in series so that it can pass the solenoid valve And time relay to control the glue feeding time and glue amount of each hot nozzle separately, make necessary preparation for injection moulding machine.
-
3. The cooling and heating system of the Auto light mould
-
When the plastic material is injected into the mould cavity, within a reasonable temperature range, the higher the temperature of the mould cavity surface, the better the surface quality of the product and the lower the internal stress of the product. Therefore, to obtain good product surface quality, it is a good way to increase the surface temperature of the cavity. Generally, the light mould is heated by a mould temperature machine during injection moulding, so that the plastic is kept at a high temperature in the mould, and the temperature is reduced, thereby eliminating defects such as flow marks and weld marks, and achieving a mirror effect.
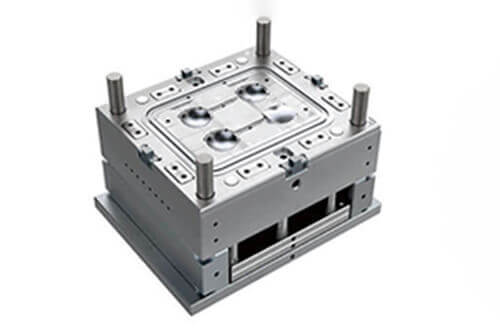